Previously, the only way to create “wood” was to grow trees…
For thousands of years, natural wood has been an indispensable part of human life, used in buildings and furniture. Wood, formed over long periods, possesses the necessary hardness and workability for structures. To obtain wood, one must grow trees and cut them into desired shapes. However, using cylindrical trees as squared timber results in waste. There are composite materials like balsa wood, assembled from these pieces, but they have issues like being prone to breakage or lacking elasticity due to the use of adhesives.
Thus, researchers pondered: could we not 3D print “wood”?
Three-dimensional printing of wood
How to Make 3D Printed Wood
The smallest structural component of wood is called microfibrils, which are bundles of cellulose chains that have both crystalline and amorphous regions, covered with lignin. Its composition includes cellulose-based carbohydrates (about 70%) as reinforcement, lignin (about 25%) as the continuous phase, along with other trace components.
3D printed wood mimics the composition of natural wood, consisting of lignin, crystalline cellulose, and amorphous cellulose. These mixtures are combined with water and extruded through a syringe with a fine tip to form shapes. The printed wood, just after extrusion, contains water and is brittle, lacking a crystalline structure. Therefore, the water is removed through freeze-drying, and the material is then heated to 180°C to melt and recrystallize the lignin. This process fills the voids left by the removed water, creating a hard structure. Furthermore, applying pressure during heating increases the density, resulting in 3D printed wood that is closer to “natural wood.”
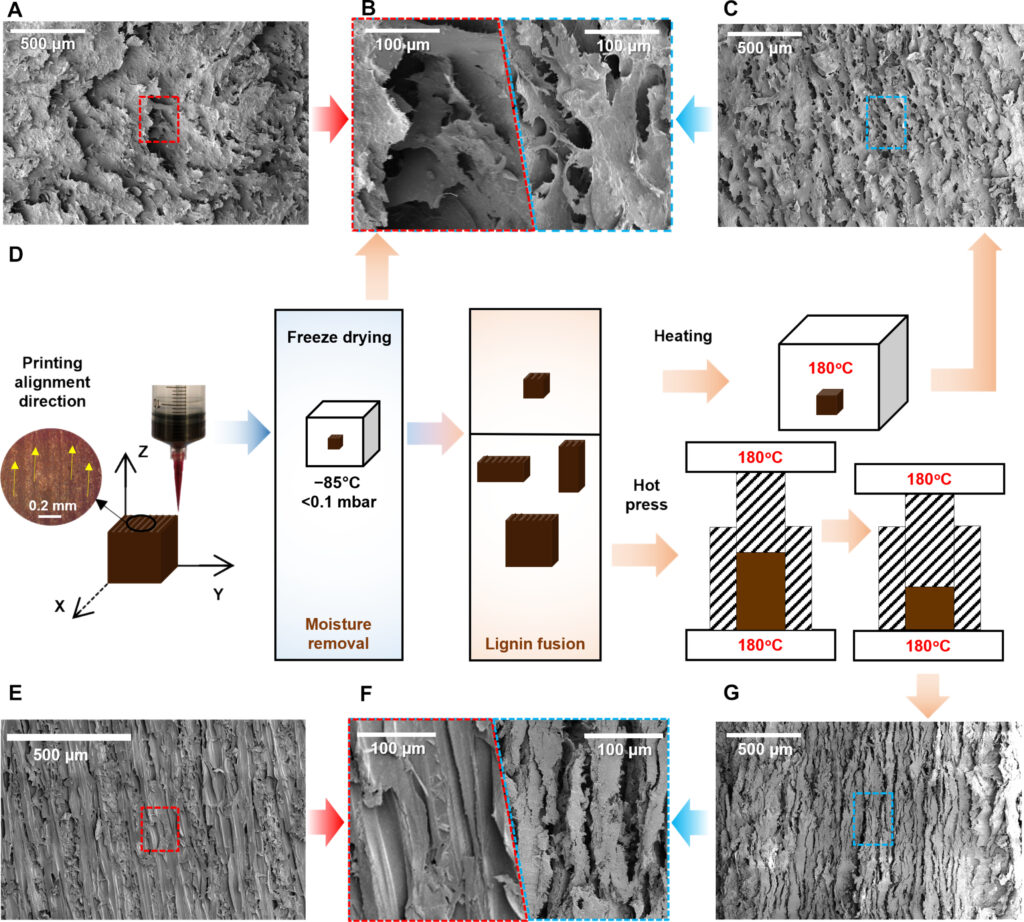
Remarkable Properties of 3D Printed Wood
The 3D printed wood created in this way exhibited characteristics comparable to natural wood. The pressurized printed wood had flexibility similar to natural timber, with a fracture toughness twice that of natural balsa wood and 1.5 times the bending elasticity. This indicates that it has properties closer to wood than composite materials.
Moreover, the resolution during extrusion is an impressive “200μm.” While creating three-dimensional objects from wood typically involves carving, with printed wood, molding is also possible, potentially allowing for more complex shapes.
Creating “wood” from non-wood materials.
A notable feature of printed wood is that it doesn’t need to be derived from wood materials. The raw materials for printed wood are lignin and cellulose, which are not exclusively obtained from wood. Lignin can be sourced from vascular plants like cotton and hemp. Cellulose can be produced by organisms like bacteria and fungi or derived from agricultural waste. Using these sources, it becomes possible to produce printed wood without the time constraints of growing timber.
The Challenge of Energy Cost
The drawback of printed wood is its high energy cost at present. Freeze-drying requires energy for both the low-temperature process and for reducing pressure. The subsequent pressurizing and heating steps also consume energy. If research progresses in reducing costs, the demand could be high, as it would allow for easily obtaining desired wood shapes. However, currently, using actual wood is likely more cost-effective.
Recently, it has become possible to print houses using 3D printers, with cement as the building material. If research on printed wood advances, it might be feasible to use printed wood instead of cement, potentially realizing the concept of 3D printed log houses.
コメント